How to Properly Perform Roofing Installation
A roof protects a home from the blazing sun, pounding rains and gusting winds. When it’s time to replace or re-shingle your roof, you have many options.
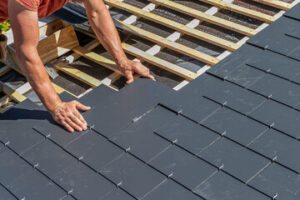
Your contractors will lay tarps to protect your yard and lawn from debris, and will park a dumpster in your driveway for easy access. They’ll also inspect and repair flashing, the material that seals joints like those around a chimney or vent. Consult with Palm Coast Roofing Companies for expert guidance.
When it comes to roofing materials, the choice depends on a variety of factors. A cost versus durability comparison is important, as are the effects of climate and energy consumption. A roof can be made from a variety of materials, including metal, asphalt shingles, and slate. Clay or concrete tiles add texture and beauty to a house, but they are expensive and require special framing.
Rolled roofing is a standard choice for low-slope residential roofs and outbuildings like sheds and garages. It consists of long rolls of mineral-impregnated and asphalt-impregnated material topped with mineral granules. Unlike shingles, which are applied one at a time, this type of roofing is rolled out and then nailed down. Rolled roofing is cheap but does not offer much in terms of aesthetic value. It should not be hammered down on flat roofs as this can cause leaks.
If you have a steeper slope, you can choose a built-up or membrane roof system. These combine the advantages of a flat roof, such as being walkable and durable against snow, with the traditional granule look of a shingled or a tiled roof. The membrane is usually coated with a layer of bitumen, which acts as the waterproofing barrier. This is often reinforced with a layer of fiberglass or polyester to increase its strength and permeability.
There are also synthetic rubber membranes such as EPDM (ethylene propylene diene monomer), which is an environmentally friendly material. However, these don’t have the insulating effect of shingles.
A newer option is solar shingles, which are a green roofing alternative that generates electricity for a home. While this renewable energy source does have a high upfront price tag, it can help reduce heating and cooling costs and cut carbon emissions.
Before starting any roofing project, you should gather the necessary tools and materials. A hammer and nail gun can speed up the installation process, as will a utility knife to cut the underlayment and shingles. A chalk line will help you create a straight mark along the rooftop so your shingles are applied in a symmetrical manner. Lastly, you will need roofing cement to adhere the underlayment and the shingles.
Installation Methods
The roofing installation process varies depending on the type of roof. For instance, a flat or low-sloped residential roof is much different than a steep sloped commercial roof. The process is also affected by the material used for the roof, which can range from asphalt shingles to metal panel roofing. Regardless of the roofing materials used, the contractor will follow the manufacturer’s guidelines for installing the product to ensure proper protection from the elements.
After a thorough inspection of the existing roof, your contractor will start by removing any debris and clearing the work area. They will lay tarps around shrubbery and movable sculptures to protect them from damage, as well as on driveways or garages to prevent stains. They will then park a dumpster on your property and sweep the roof surface to remove any loose or fallen materials.
Once the roof is clear, your roofer will install a new underlayment and flashing. The underlayment is a layer of felt, rubber or fiber that covers the entire roof decking to help prevent water from seeping under the shingles and damaging the structure of your home. The roofer will also install flashing–metal sheets–around the corners of your roof, at skylights and chimneys, along all peaks and drip edges, and over any areas where the new shingle roofing will overlap other areas of the roof.
The next step is to install the new shingles. AKVM’s experienced roofing crew follows Owens Corning’s strict installation methods to guarantee that your roof will be covered by the manufacturer’s warranty. The crew will tear off the old shingles, using pry bars and a utility knife to carefully peel them away from the underlayment. If the underlayment is still in good condition, it will be saved and put back over the new shingles.
If the underlayment or flashing is in poor condition, your roofer will remove them and replace them as necessary. They will also add an ice and water barrier to the roof, if needed. The crew will then run the underlayment across the roof, over the ice and water barrier, and over the drip edge. Then the new shingles will be installed, starting at the eave and working in rows up to the ridges.
Underlayment
Underlayment is a crucial part of your roofing installation. It acts as an added layer of protection from rain and other harsh weather, keeping your shingles safe and helping to prevent moisture damage. There are several different types of underlayment, including felt, rubberized asphalt, and synthetic materials. The type you choose depends on local building codes and regulations as well as your specific needs and the climate in your area.
The underlayment is placed on the roof deck directly before the roofing material, and it provides a moisture barrier for the outer layers of the roof. The underlayment also helps to support the shingles, which is essential for the integrity of your home’s roof. Depending on the weather in your area and your home’s layout, you may need an underlayment that can repel water or help with drainage.
Felt underlayment is one of the most common forms of underlayment, and it’s typically made from an organic mat or paper that’s saturated with asphalt to help with waterproofing. Typically, the underlayment is nailed down with a row of nails every four to six inches along the edges and less frequent along the middle. This pattern is repeated for each row of underlayment until it’s up to the roof’s ridge.
Another option is a rubberized underlayment, which can provide more insulation than traditional felt underlayment. It’s also easier to work with, especially in cold temperatures, as it can shrink and stretch without breaking. The upper surface of the underlayment can be coated with granulated polyester or polyethylene, providing extra weather resistance. It can also have a nonskid surface, making it easier for roofers to walk on during installations.
There’s also a newer generation of underlayment made from various synthetic materials, which can be more durable than asphalt underlayment and don’t degrade as easily. These can be nailed down using the same method as felt underlayment, although some manufacturers advise that the use of synthetic underlayment can affect certain product warranties for the outer roofing material.
For all underlayments, it’s important to follow the manufacturer’s recommended fastening schedule. When nailing down the underlayment, be sure to use button cap fasteners, which are much stronger than traditional roofing nails and can resist high winds. It’s also important to make sure the underlayment is free of debris and damaged areas before installing any other materials.
Plywood
The plywood used in roofing installation comes in a variety of thicknesses and grades, but it’s important to consider what kind of project you’re working on before buying the material. Depending on your application, you might need a grade of plywood that’s smooth enough for cabinetry or strong enough to withstand structural pressure. You also need to choose a material that’s affordable, but not too cheap that it will compromise the quality of your finished product.
Plywood is an engineered wood made from multiple layers of veneer glued together. The amount of layers, or plies, determines the thickness of the plywood. Different types of plywood are available for use in a wide range of applications, including flooring, walls, and roof sheathing.
Before purchasing plywood, carefully examine the sheets for defects and blemishes that could affect the finish of your project. Look for cracks and dents, as well as any inconsistencies or irregularities in the veneers. You should also make sure that the edges of the sheets are sealed, as this will prevent moisture from infiltrating the edges and causing warping or shrinkage.
A Plywood Manufacturing Process
The production of plywood is an extensive process that involves multiple stages. The choice of logs, the precision with which the veneers are peeled, and the type of adhesive used in each step all contribute to the final quality of the product.
First, high-quality logs are selected. These are typically from softwoods like pine and fir, but they can also be from hardwoods like birch. They are then debarked and cut into long ribbons. These ribbons are then conditioned, soaked in vats of hot water, and cut into pieces that are then dried. These pieces are then glued together using an adhesive that is typically either phenol-formaldehyde or urea formaldehyde. The resulting ply block is then pressed under high heat and pressure to form a strong bond.
The result is a sturdy material that’s more stable and flexible than solid wood, making it ideal for roofing and wall sheathing. It is also less prone to warping, shrinking, and splitting due to changes in humidity or temperature. It is also easy to work with, and it can be trimmed down to size with power tools. However, exterior plywood can be more susceptible to damage from sunlight and rain, so it is important to seal or finish it properly when using it outdoors.